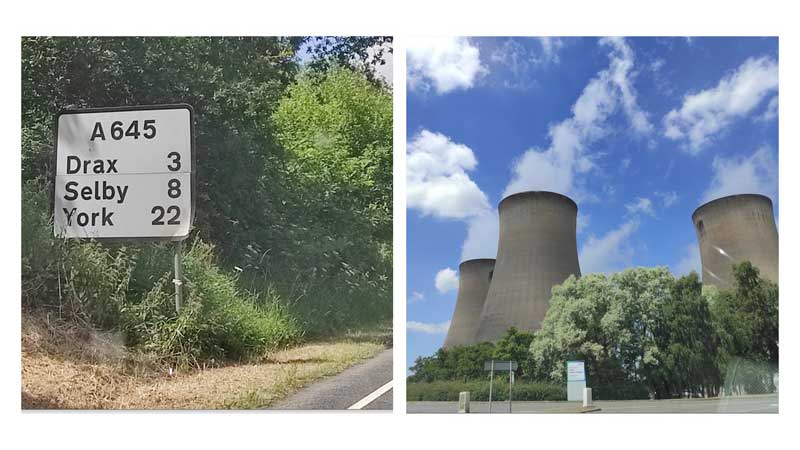
On June 22, 2022, Florian Auclair and Jean-Pierre Deflandre took the opportunity to visit the Drax biomass plant. This plant located in Yorkshire, England, aims to become the first full BECCS installation in Europe.
If successful, this project would be remarkable for at least two reasons. First, the plant is truly massive, capable of producing about 400 MW of electricity. That's nearly 8% of Britain's total consumption. Second, its conversion from coal to biomass in a decade is a virtuous example for the decarbonization of industry. In 2000, the plant was one of Europe's biggest polluters, emitting 21 million tons of CO2, and by 2030 it could be capable of storing 8 million tons of negative emissions.
Before arriving, we could already see, from several kilometers away, the 12 impressively high cooling towers that were used to cool the 6 coal-fired boilers.
Today, 4 boilers have been converted to burning wood pellets and the former coal stockpile is now completely flat and empty. The fuel stock is now handled by 4 storage spheres, each of which holds up to 2.5 days of consumption.
On arrival, we were greeted by a large 3-dimensional model of the power plant and were able to appreciate the gigantic size of the plant. After explaining the location and role of each building, we were shown a huge wall map of North America on which we could locate the various pellet production plants owned by Drax. By developing its own supply chain, Drax secures its access to fuel and by selling the surplus, it hopes to generate additional revenue.
Next, we were invited to equip ourselves with headsets, safety jackets and helmets before walking through a huge hangar that houses turbines, boilers and mills. As we went out of the hangar, we were driven to the biomass storage and unloading areas.
The whole production process starts from the storage spheres, which are filled daily by about 20 specially designed and chartered trains that unload their pellets cargo onto conveyor belts, while moving slowly. The pellets are then transported again by a conveyor belt to a mill (consisting of 4 huge rotating steel balls). There, they are crushed to facilitate combustion. The resulting dust is continuously sprayed into the boilers to produce high pressured steam. From each boiler, the steam is then passed through various circuits connected by heat exchangers (some of them can contain up to 300 kilometers of pipes). In each circuit, 3 different types of turbine on a single shaft are activated following the pressure decrease. The whole shaft turn the alternator that produces at the end, the electricity.
The carbon capture process is currently only effective on one boiler and remains at an experimental level, but the company plans to expand the capture to other boilers as soon as possible. The space for compressor stations is already prepared to export carbon emissions to the North Sea, to the Endurance offshore field. However, there are still substantial barriers ahead of delivering this CCS project. The funding for these structures is uncertain and the business model for negative emissions is unknown.
Currently, Drax relies heavily on state subsidies to remain profitable but this revenue sources will be extinct by 2027. If no plan is found to fund negative emissions, this BECCS conversion could be halted.